Royal Museums Greenwich is home to the National Maritime Museum, Royal Observatory Greenwich, historic ship Cutty Sark and the Queen's House.
The museum collections include over 2.5 million items and offer a window into maritime life, scientific enquiry and artistic achievement.
Browse online articles, hear from museum curators, astronomers and special guests, and take a deep dive into our collections and archives.
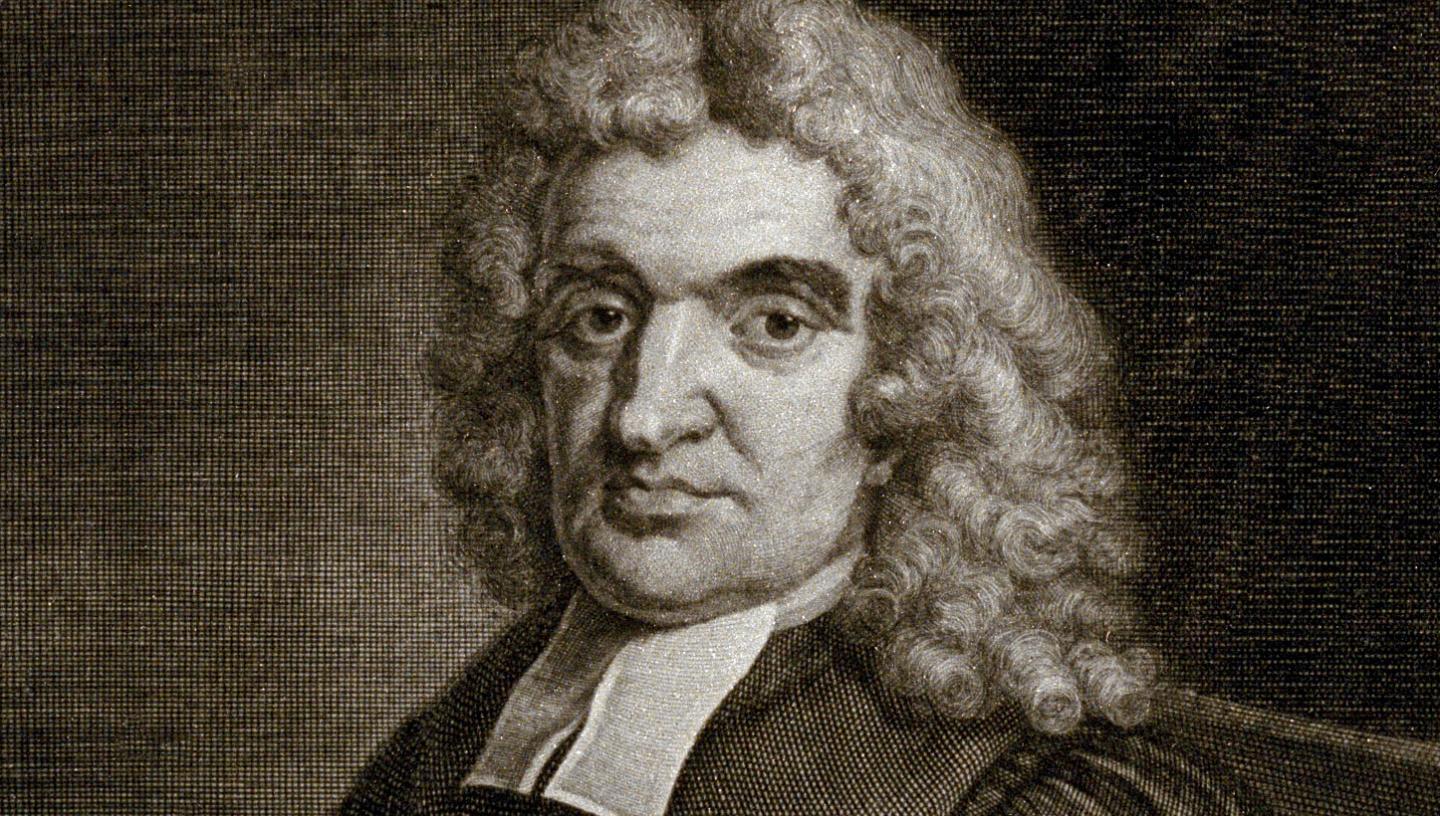
Featured story
This is John Flamsteed, the first Astronomer Royal and a pioneering scientist. Why did his spectacular feud with Isaac Newton shape the early history of the Royal Observatory?
Search the collection
Explore our digital collections or visit our library, archive and collections studio in person
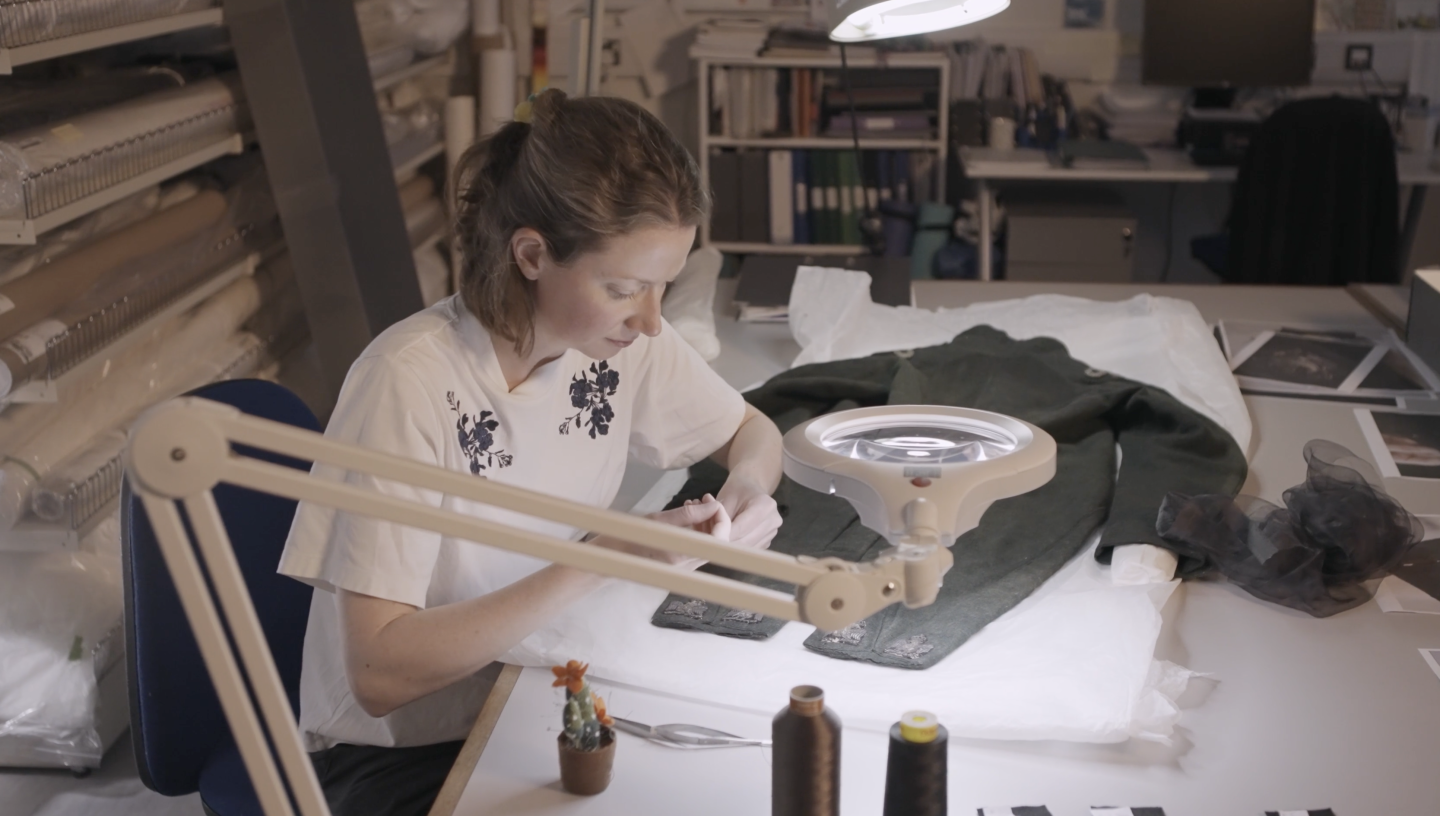
Support stories like these
Royal Museums Greenwich is a charity, and we rely on your support to care for our collections and allow everyone to discover the wonders of space, time, history and creativity. Donate today and help shape the Museum's future.